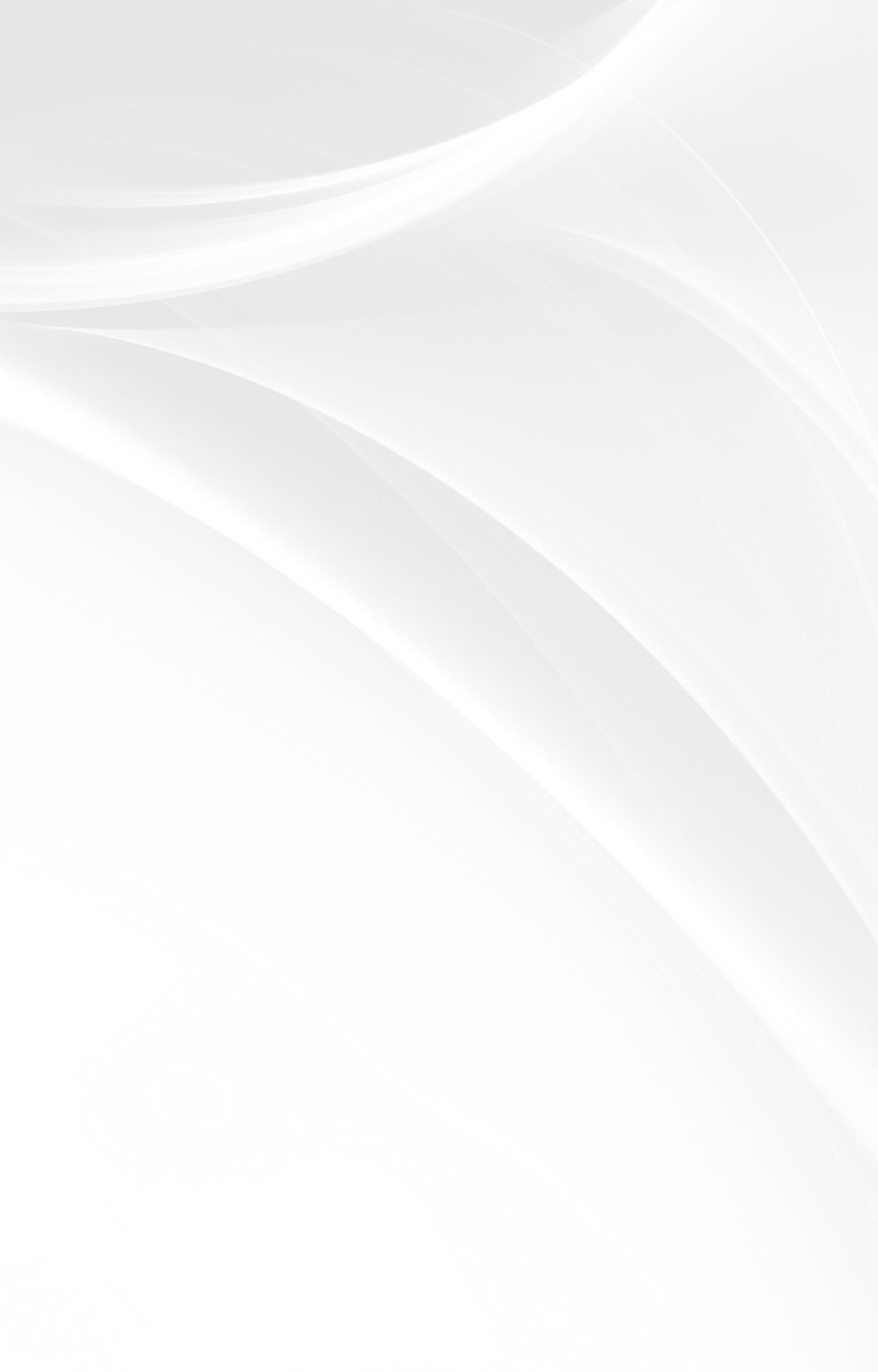
CPC4000FA Deburring Machine
Powerful Versatility, Fully Automated
The CPC4000FA is the fully automated model of the CPC4000 deburring machine. It includes a media elevator as well as a media, water, and optional liquid compound fill system. Media is stored in a hopper above the main unit to allow for quick process turnaround and eliminates heavy lifting. The CPC4000FA reduces downtime by keeping media in the system, allowing operators to continuously run processes. Just like all the other systems offered by United, the CPC4000 comes standard with PLC and touchscreen controls and an internal separation and rinse system. The CPC4000 can process parts up to 27.5" long. The urethane barrels can be divided into up to 10 separate compartments and can be adjusted to meet any deburring or mass finishing needs. Generates up to 22Gs.
Features
The CPC4000FA is the fully automated variant of the CPC4000HD. Its media elevator and hopper system automates loading for the operator. The media, water, and compound metering systems make filling barrels easy and consistent. These systems reduce loading and unloading times, making room to run more processes throughout each shift.
The FA attachment is designed to be added at any time. All the connections, including water and electrical, come with quick connects for seamless and effortless connection by the customer
The CPC4000's drive system is configured in United's butterfly design and is composed of heavy duty chains to eliminate stretching. Power locks prevent slippage or premature wear on sprockets. United's drive system is durable and easy to maintain. All maintenance can be performed by removing a side panel with just 4 screws.
The use of an injection-molded urethane liners allows the customer to replace barrel liners quickly with minimal down-time. Cradles can be fitted with dividable liners. These liners contain slots for 9 dividers which create up to 10 compartments within each barrel.
The CPC (Computerized Process Controller) is capable of storing a large amount of process information such as: types and amounts of media and compounds, maximum number of parts per barrel, loading instructions, and cycle time and turret RPM. The operator may choose which process to run (either by part description, part number, or process code) from the preset process screen, then simply select either to review operating procedures or to run the process.
The CPC4000's automated rinse and separation system separates and rinses parts and media through the use of interhangeable stainless steel separation screens which can be ordered in different sizes and be easily changed. The CPC4000 eliminates the need to remove barrels from the machine to access parts and media. Simply remove the lid and dump contents into the material handling system. Parts can be separated from the media through screens while they exit the machine separately.
Touchscreen Controls
User-friendly touchscreen display.
Process storage capabilities.
Process countdown timer.
Full Automation
Media lifting system with hopper storage.
Water & Compound metering and filling.
Safety
Two-handed jog operation.
Door lock prevents door from being opened while machine is running.
Emergency stop button.
Variable Speed
Up to 200RPM
Process versatility.
Gentle on delicate parts.
Barrel Liners
Divided option available, standard.
Easy relining - no need to disassemble machine.
Fully Integrated Motor Controls
Easy to operate.
Safe - operator has no access to line voltage.
Improved motor protection.
Removable Body Panels
Easy access for maintenance.
Replaceable panels, no need for bodywork or welding.
Easy cleaning.
Stainless Steel Construction
Prevents corrosion from moisture.
Equipment lasts longer.
Urethane Barrels
Greater traction increases energy transferred to the media.
Greater process efficiency.
Improved heat resistance.
Barrel Locks
No tools required to open barrel.
Increased operator convenience.
Reduced reloading time.
Warranty
Up to 3 years, determined by component type.
Complies with ANSI/NFPA 70 and NFPA 79 Codes UL Approved
Nationally accepted safety standards.
Trusted safeguards for operators and equipment.
Standardized design.
Specifications
Total Capacity
4 Cubic Feet | 112 Liters
Barrel Capacity
1 Cubic Foot x 4 Barrels
Barrel Dimensions
D 8.5” x W 27.5” (internal)
Machine Dimensions
D 65” x W 91” x H 122”
Max Capacity
10, 2½” Compartments per Barrel, 40 Total
User Interface
Touchscreen with Process Storage
Main Drive/Motor
10HP, Inverter-Controlled, Three-Phase
Turret Speed
0-200 RPM, Fully Adjustable
Operating Volume
~80 Decibels
Construction
304 Stainless Steel
Power Requirements
380VAC-480VAC, 50/60Hz, 3Ø, 30A UL certified
Water
Required for fill hose.
Compressed Air
80-100psi
Dry Floor Compatible
Yes
Warranty
Up to 3 years, determined by component.
Options
Extra Barrel Liners
Separating Barrel Lid